A White Paper Review: History of Use and Performance of Copper Tube For Potable Water Service
Richard O. Lewis, P.E.
Lewis Engineering and Consulting, Inc
Introduction
The hot and cold potable water distribution piping in the typical U.S. residence is generally of little concern to the homeowner or apartment resident. Hidden behind walls, ceilings, floors and cabinets, it is mostly out of sight, and fortunately is rarely a problem. The most common domestic water problems encountered are dripping faucets, sticking or leaking toilet tank valves and occasionally a water heater that ceases to work properly. These are nuisance problems that most every homeowner has experienced at least once. By comparison, more serious and damaging water supply problems associated with pipe leaks are far less common. When they do occur, however, leaks can result in extensive water damage if not immediately detected, and often expensive repairs.
What are the principal causes of water pipe failures and can the average home owner detect potential problems before they become serious? There are a number of factors that affect the performance and service life of water pipe, or tube, that must be considered: (1) the size and type of pipe, or tube, material installed, which in a U.S. home is most likely copper, but may also be galvanized steel or plastic pipe, such as PVC/CPVC or polybutylene, (2) the design and workmanship of the installed piping system, (3) the quality, or corrosiveness, of the water conveyed in the pipe, and (4) the current age of the pipe. Each of these factors must be considered when evaluating the current condition, or the cause of leaks, in a home water piping system. The following discussion is intended to provide basic information for the homeowner about the known causes of plumbing failures and leaks.
Background
Although water piping in homes may be any one of the several materials mentioned above, market data surveys by the Copper Development Association (CDA) [1] confirm that copper is the predominant material selected for domestic water service and distribution in residential construction. Water service is defined as the pipe from the meter or main to the building, and distribution as the water plumbing within the building. Copper became a popular choice for water distribution plumbing in the U.S. following World War II, but had been available since the 1920's with the advent of solder fittings for joining pipes [2]. Market data compiled and published by the CDA in the early 1980's reflecting the production and sale of copper water tube reported more than half a billion linear feet of copper water tube installed annually [1]. By 1994, that amount had increased to about one billion linear feet per year in U.S. water service and distribution systems [3]. This accounts for more than 80% of the total water distribution pipe installed in residential construction. The continued high volume usage of copper tube for hot and cold water plumbing is indicative of the problem free performance obtained by most homeowners.
A useful starting point for examining the use and performance of copper tube for water distribution is the material itself and the methods of installation. Practically all copper tube for water service is manufactured according to American Society for Testing and Materials (ASTM) standard B88, Standard Specification for SEAMLESS COPPER WATER TUBE [4]. This nationally recognized standard, first published in 1932, defines the product forms, chemical composition, dimensions, tolerances and overall quality of the finished products. Copper tube dimensions are specified according to a nominal diameter for which the outside diameter of any size from 1/4 inch to 12 inch is one-eight inch larger than the nominal diameter. Of interest to the home owner is the fact that copper tube is available in two product forms, hard drawn straight lengths and soft annealed coils.
Each product form is manufactured in three types. The primary difference in the three types is wall thickness, with Type K having the thickest tube wall, Type M the thinnest, and Type L having an intermediate thickness.. For example, a very commonly used standard size in home plumbing, 2 inch, is 0.625 inch outside diameter. In Type K, 2 inch tube has a specified nominal wall thickness of 0.049 inch, compared to only 0.028 inch nominal thickness for Type M.
Hard drawn straight lengths of tube are required to be identified by the manufacturer with stenciled markings along the length of the tube in green for Type K, blue for Type L and red for Type M; no markings are required on soft annealed coils. By inspection of new tubing, one should be able to readily identify the manufacturer, country of origin and size and type of copper tube provided. Those markings can deteriorate and become difficult to read, however, as installed tubing ages.
Nationally recognized plumbing codes, plus local jurisdiction construction codes and ordinances, are combined in any locale to specify and regulate acceptable practices for installation of plumbing by licensed contractors. Proper construction and installation of copper water plumbing is highly dependent on the skill and workmanship of the plumbing contractor in assembling and joining copper tube to the fittings and valves necessary to construct a distribution system. Soldering is the most widely approved method employed. ASTM B828, Standard Practice for Making Capillary Joints by Soldering of Copper and Copper Alloy Tube and Fittings [5] defines, and describes in detail, the correct procedures to consistently make satisfactory joints.
Copper Corrosion Resistance and Performance
Documented incidents of leaks in copper water tube are rare when compared with the total amount of copper water tube installed in the U.S. homes and apartment buildings [1]. With few exceptions, the leaks originate on the inside (waterside) tube surface. The process responsible for the formation of leaks is corrosion, defined for practical purposes as oxidation and consumption of metal. All metals and alloys of commercial importance, including copper, but with the exception of the precious metals such as gold and platinum, will naturally revert from their metallic form to an oxide if exposed to the proper conditions. Copper alloys are relatively corrosion resistant by virtue of protective films that form as the copper ages. The darkening of a new copper penny, or the gradual formation of a blue-green (verdigris) patina on ornamental copper objects exposed out-of-doors, are examples of protective film formation on copper that most everyone is familiar with.
Plumbing system engineers and designers most often select copper because of its history of good performance. A conservative service life of 20 years is generally assumed for design purposes, but an actual life of 25 to 30 years, and more in some areas of the U.S., is usually obtained. Achieving a long, problem free service life from copper water tube is dependent upon the formation of a uniform, protective film on the inside of the tube. A slow rate of uniform corrosion that begins when water containing dissolved oxygen is first introduced into the plumbing system is responsible for formation of the protective film. Depending upon the source of water and water treatment, the film is a mixture of copper oxides and calcareous mineral scale. The protective film creates a barrier between the metal surface of the tube and the flowing water. As the protective film develops during the initial few months of use, the corrosion rate decreases from an initial value of 0.001 to 0.003 inch per year on the clean metal surface to a long term average rate of 0.0003 inch per year. The long term corrosion rate value, according to the American Water Works Association [6], is typical for copper tube in potable waters containing dissolved oxygen and a pH between 7.0 and 9.0. Any physical or chemical condition that interferes, however, with the initial film formation process, or results in damage to the film, can cause accelerated pitting type corrosion and short term failure of the copper tubing. Short term failures generally occur within 1 to 6 years of placing the plumbing system into service [6, 13].
In response to environmental concerns about water quality in general, and drinking water specifically, the U.S. Environmental Protection Agency (EPA) was empowered by the U.S. Congress with oversight and enforcement responsibilities in the Safe Water Drinking Act (SWDA) of 1973 [7]. Amendments were passed in 1986 [8] that further defined water quality requirements, and eliminated the use lead in solders for joining copper tube. In 1991 [9], Congress further amended the SWDA placing maximum contaminant level (MCL) restrictions on the amount of lead and copper that could be present in public utility supplied drinking water. Commonly referred to as the ALead and Copper Rule,@ procedures were defined in the amendment that require utilities to monitor and report the quality of water provided, and the actions to be taken if the water fails to comply with the MCL requirements. Water quality reports published by the public utilites, as required by the USEPA and the SWDA, can be obtained by the home owner. They provide information useful in judging the quality of potable water delivered to their homes and the effect that water likely has on their copper plumbing.
Corrosion Failures: Causes
Published accounts of copper water tube failure investigations and research studies [1,2,3,6,11,12,13,14,16] during the past more than 40 years have identified several design, installation and water chemistry conditions that have been found responsible for the occasional failures. Water is the essential element to any internal tube or pipe corrosion problem, but there are several design, installation and initial operation factors that can be the primary cause of leaks and failures.
Water Chemistry Effects
The source of raw water and the treatment methods applied by public utilities to produce potable water for distribution to it=s customers determines the taste, odor and corrosiveness of the finished water. Raw water sources vary dramatically across the U.S. A primary distinction is made between surface water collected in reservoirs from rain or snow-melt, or from rivers, and well water pumped from underground aquifers.
Surface Water Sources
Surface waters from rivers and lakes usually have a total dissolved solids content less than 100 milligram per liter (mg/l) and are characterized as soft (calcium and magnesium content less than 50 mg/l) and low in alkalinity (total amount of bicarbonate, carbonate and hydroxide less than 50 mg/l) [15]. These values are very general, and significant variations exist for different geographic areas of the U.S. In the Pacific northwest, for example, the principal raw water source is surface water from snow-melt which has a total dissolved solids content of 30 mg/l, or less, is very low in alkalinity and hardness, and is highly acidic.
For reference, acidic implies a pH of less than 7.0. A neutral pH is defined as 7.0, which is neither acidic nor basic. At a pH less than 7.0, soft low alkalinity surface water can promote unacceptably high corrosion rates on copper plumbing. Besides complaints by customers of green staining of porcelain plumbing fixtures, improperly treated water can lead to violations of the SWDA Lead and Copper Rule. Corrosive water of this type must be treated with lime, soda ash or caustic soda to increase the alkalinity and raise the pH above 7.0, which effectively prevents general corrosion of copper plumbing [2,6].
Raw surface waters generally require treatment to remove suspended matter. A flocculating agent, such as alum (aluminum sulfate), is added to promote coagulation of the suspended matter for removal in sedimentation basins at the treatment plant. For many surface waters, filtration is also necessary for sediment removal. Carry over of suspended material and alum in the finished water can occur, however, and has been identified in some case histories [11] as a contributing factor in preferential pitting of hot water copper tubing. Deposition of aluminum hydroxide, and other materials such as manganese dioxide and hydrated hematite (iron oxide), on the surface of copper tubing have been identified as pitting agents in hot water plumbing.
Groundwater Sources
The most widely publicized corrosion problems with copper plumbing [1,2,3,14] have occurred in treated and untreated water pumped from wells. Groundwater, as compared to surface water, is generally hard and alkaline, with a total dissolved solids content of 200 to 300 mg/l, or higher. Significant amounts of dissolved carbon dioxide are often present in groundwater, which if not properly treated, can be extremely aggressive to copper tube. The effect is most commonly referred to as Acold water pitting,@ and is characteristically observed in cold water plumbing, but not in hot. Pitting under these conditions is less sensitive to the effect of gravity, and as a rule, does not occur preferentially on the bottom of horizontal tubing, but rather, is distributed around the entire inside surface of the tube. Cold water pitting can be very aggressive, penetrating the tube wall in a relatively short time, but usually within three to four years after being placed in service. The frequency of leaks typically decreases after five years, and is rarely observed after 15 years or more.
Pitting is almost always associated with hard well waters with pH values in the range from 7.0 to 8.2 [2]. NACE publication TPC No.7 [12] describes well waters having pitting tendencies are characterized by a pH of less than 7.8 and containing more than 17 milligram per liter (mg/l) of carbon dioxide. Well waters treated to raise the pH to 8.0, or above, to remove dissolved carbon dioxide are generally rendered non-corrosive to copper. Aeration is also an effective means of removing dissolved carbon dioxide, and has the added benefit of stripping dissolved hydrogen sulfide from the water, when present. Well waters in some areas of the U.S. contain hydrogen sulfide which not only causes an offensive odor problem, but also promotes cold water pitting of copper water tube. Treatment schemes to remove hydrogen sulfide generally rely on a combination of chlorination and aeration.
Design and Installation Factors
Soldering Flux Induced Corrosion
Application of excess soldering flux during fabrication of soldered joints has been found to be a significant cause of corrosion failures in copper water tube [16]. ASTM B828 describes the proper procedures for preparation and joining tube ends to fittings by soldering. The standard warns against careless workmanship that can cause problems long after the system has been installed. Heat applied during soldering melts the flux to clean the surface for bonding of the solder. If excess flux has been applied, the heating process can result in the flow of melted flux on the inside of the tube and fitting. Lead-free solders mandated by amendments to the SWDA in 1986, are more difficult to use correctly compared to traditional lead-tin solders, and have probably contributed to overzealous use of flux in some cases.
If the entire plumbing system was flushed with hot water during testing and commissioning, most of the commonly used petrolatum based flux would be dissolved and discharged to the drain. Cold water in the cold water plumbing, however, does not effectively dissolve or remove the flux from the tube surface. Rather, the flux remains primarily where it was originally deposited, although some of the flux is gradually dispersed and redeposits on the tube downstream of the soldered fitting. Leaks due to pitting corrosion typically develop after one to five years, in and around the flux deposits in the cold water plumbing. Leaks due to flux induced pitting are most common along the bottom of horizontal tubing.
The following discussion is a case history example of flux induced pitting corrosion in 3/4 inch copper cold water tubing after six years service. The inside surfaces of companion hot and cold water copper water tube samples from the same location were examined by splitting each sample lengthwise. The cold water section at a soldered joint is shown in Figure 1, and at a location 48 inches downstream from the joint in Figure 2. Pitting corrosion was observed beneath each of the dark green mounds, or nodules, primarily on the bottom of the horizontal section of tube. Nodules and pitting corrosion were visible for more than 10 feet downstream from the joint.
By comparison, the companion hot water tube from the same location shows evidence of where excess flux had been deposited near the soldered joint in Figure 3, but there was no evidence of pitting corrosion at that location, or anywhere downstream. The inside surface of the tube at a distance of 18 inches downstream, which is typical of the entire 10 feet of tube removed, is shown in Figure 4.
The effect of residual flux on the inside of cold water tube is evident in the 3/4 inch diameter tubing section shown in Figure 5 removed from a vertical location in an apartment plumbing system. Residual flux was confirmed in deposits around the full circumference of the tube sample. Half of the tube after cutting, at the top in the photograph, was left with the flux and corrosion product film intact. The mating half, at the bottom, was cleaned to remove deposits and expose the copper surface. A pattern of pitting corrosion is evident where flux and nodules had been present prior to cleaning.
|
|
Inadequate Flushing and Stagnant Water
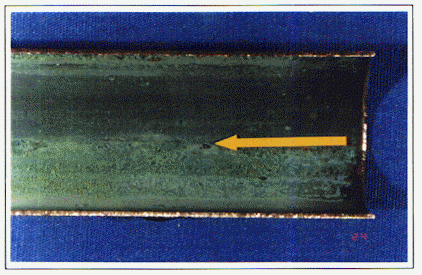
Formation of a uniform, protective film on copper also depends upon proper flushing of the system to remove construction debris from the inside of the tubing. Clean inside surfaces are essential to the development of protective films. If debris is allowed to remain in place on the inside surface for an extended period of time early in the life of the system, two to three months for example, corrosion can develop beneath the deposits [6,14]. Once started, this type of Aunder deposit corrosion@ will likely continue resulting eventually in a leak failure.
A related cause of copper corrosion can occur when a completed plumbing system is allowed to remain stagnant with residual water for an extended period of time following flushing and testing. This problem has been discovered and identified most often in tract homes and apartment complexes that are often constructed, but not occupied, for a period of time [13]. The initial stages of protective film formation on a clean copper tube surface depend upon a frequent flow of water through the system to promote uniform film growth. Stagnant conditions for extended periods of time, especially when the system is partially filled, can cause non-uniform film development and corrosion depending upon the source of water.
An example of stagnant water induced corrosion is shown in Figure 6. The copper tube sample shown is from a horizontal section of 3/4 inch Type M cold water tube removed from an apartment complex that had been tested for leaks, but remained unused for several months. After two years, leaks began to develop in the plumbing. The upper half of the tube is positioned at the top in the photograph. A residual amount of water remained in the tube following testing, resulting in the growth of a non-uniform corrosion film in the bottom half of the tube. The yellow arrow indicates pitting corrosion that occurred at the water line under the stagnant conditions. This is another example of under deposit corrosion.
Water Velocity and Erosion Corrosion
As has been emphasized, copper water tube is highly dependent upon the formation and maintenance of a protective film on the inside to provide a long trouble free service life. The film is not hard and abrasion resistant, but rather soft and easily damaged. A copper water distribution system should be designed so that the water velocity through the tubes is within the range of 5 to 8 feet per second (fps), depending upon the tube size and the water pressure. For the smaller tubing sizes normally installed in home plumbing [10], the design velocity should be targeted toward the bottom of the range. If the available water pressure exceeds 80 pounds per square inch (psi), the velocity should be maintained in the 4 to 5 fps range [11]. An even more conservative recommendation limiting water velocity to a maximum of 4 fps has been published by the National Association of Corrosion Engineers (NACE) [12].
As one would expect, the greatest effect of velocity occurs where the water is forced to change flow direction, such as at elbows and tees, but excessive water flow rates can be damaging to the entire plumbing system. When copper tube is installed that is too small in diameter for the pressure and flow available, the resulting high flow rates can erode the protective coating creating areas of bare, unprotected copper. This effect can result in a high rate of corrosion wherever the protective coating is eroded.
The dramatic effect of erosion corrosion is shown in two examples in Figure 7 and Figure 8. In Figure 7, small residual islands of original green coated tube surface are surrounded by heavily eroded brown areas where more than 40 percent of the wall thickness has been lost. Erosion corrosion develops characteristic Ahorse-shoe@ shaped features in the tube surface where the flow is diverted around small areas of persistent protective film. The water flow direction is indicated by the yellow arrow in the photograph; the water velocity in the 12 inch Type K cold water tube was estimated to have been well in excess of 10 fps.
An example of erosion corrosion in small diameter hot water tubing is shown in Figure 8. Leaks occurred in the 2 inch Type K tube in less than one year due to a combination of erosion corrosion damaging the protective film during time periods of water use, and hot water pitting corrosion during stagnant periods. One can see by inspection of the two mating halves of the tube sample in the photograph that velocity affects the entire inside surface of a straight run section of tube and is not affected by gravity.
Failure of the plumbing contractor to properly ream and smooth the cut ends of tubing prior to soldering, as required in ASTM B828, can also cause turbulent flow and erosion corrosion. The resulting corrosion rates can be very high and result in short term failures as documented in several case history studies [11,14].
[Image]
![]() Figure 7. Erosion corrosion in 1 1/2 inch Type K cold water tube from an office building; green areas are small islands of original tube surface; velocity exceeded 10 fps, flow direction shown by arrow. |
[Image]
![]() Figure 8. Erosion corrosion failure in 1/2 inch Type K hot water tubing; water source groundwater treated by public utility; arrow indicates flow direction. |
Stray Current Effects due to Electrical Grounding
The practice of using the water distribution piping as part of the grounding system for homes and buildings has been common place for more than 80 years [17]. It has long been assumed that alternating current (AC) has practically no effect on corrosion of the piping system. It is well known, however, that direct electrical current (DC) discharge from a metallic object can cause rapid and extensive corrosion. Documented cases of stray current corrosion have always been associated with DC.
A survey of public utilities was conducted [17] requesting case history information on experience with electrical grounding and water pipes. While many utilities acknowledged that grounding currents were thought to contribute in some instances to corrosion, the problem is essentially an external pipe corrosion problem. There is no clear indication from case histories or the literature that electrical grounding of the AC system through the water piping contributes to corrosion on the inside surface of the pipes. The water on the inside of pipes represents a far less conductive and favorable path for current discharge as compared to the soil or other metal objects in direct contact with the outside surface of the pipe. Corrosion, if it were to occur due to electrical grounding effects, should originate on the outside of the water pipe rather than the inside.
Copper Pipe
Any investigation into the cause of a leak in a home plumbing system would not be complete without an examination of the copper tube itself. As with any product manufactured in large quantities, such as copper water tube, defects can occur. It is extremely rare that a defect in the wall of a copper tube would go unnoticed for an extended period of time, however. Generally, if as-manufactured holes, cracks or other defects are present, they are made evident during pressure testing and commissioning of the plumbing system. If a homeowner were to experience a leak within a few days or weeks of placing a system into service, the most likely cause would be a material defect or a poorly made fitting connection. The longer a system is operated before a leak occurs, the more likely the cause is related to poor workmanship, improper flushing or stagnation, or aggressive water chemistry.
Solutions and Recommendations
There is little the average homeowner can do to affect the performance of the plumbing system once it is tested and placed into service. The presence, or absence, of problems and leaks is dependent upon the quality of the material installed, the system design, the quality of the workmanship, and the chemistry of the potable water distributed through the plumbing. None of these are easily evaluated by simple inspection. There are, however, some tell-tale signs that the homeowner should be aware of that may indicate potential problems.
Rattling of the pipes when a faucet or tap is closed is an indication of water hammer that can be very damaging to the plumbing system. Water hammer can cause mechanical failure of joints and fittings, and damage the protective film on the copper pipe surface that is so vital to long term corrosion performance. A plumbing contractor should be consulted concerning installation of air chambers to minimize water hammer.
Green stains on porcelain fixtures are clear evidence of aggressive water and the utility company supplying the water should be consulted. Accumulation of significant amounts of sediment, especially in toilet tanks, is a possible indication of corrosion in either the home plumbing or the utilities primary water distribution system. The color and type of sediment is indicative of the origin of the material.
Chlorination is an essential element of water disinfection to prevent growth of harmful microorganisms, but excessive chlorination can be damaging to copper, especially in relatively new systems where the protective films are not well established. A persistent strong, noticeable smell of chlorine in the tap water may indicate potential damage to the plumbing system, and should be reported to the utility.
In the event of a leak, the homeowner=s first course of action will always be to stop the leak and have it repaired. If one is concerned about the cause of the leak, and whether it is an isolated problem, or potentially a chronic problem likely to exist at other locations, a simple procedure should be followed. The homeowner should gather as much information about the leak location as possible to assist in identifying the cause. The leak sample removed in making the repair should be preserved with as little damage as possible, and marked to identify, (1) the source location, (2) orientation of the leak section as installed in the plumbing system prior to removal, (3) whether from the hot or cold water plumbing, (4) the age of the section, if known, and (5) any identifying information stenciled on the side of the tube in the vicinity of the leak. An examination of the leak section by a laboratory or individual experienced in corrosion analyses can often identify the cause, or causes, and assist in identifying the scope of the problem and the most practical and effective solutions.
Prepared by:
Richard O. Lewis, P.E.
Lewis Engineering and Consulting, Inc.
July, 1999
Bibliography
- Lyman, W.S., Cohen, A., and Myers, J.R., Causes and Prevention of Pitting Corrosion in Copper Plumbing Systems in the USA, proceedings of the International Symposium on Corrosion of Copper and Copper Alloys in Buildings, presented March, 1982, Tokyo, Japan.
- Internal Corrosion of Water Distribution Systems, AWWA Research Foundation cooperative report, 1996 ed., Chapter 5, p.231-268.
- Myers, J.R., and Cohen, A., Pitting Corrosion of Copper in Cold Potable Water Systems, Materials Performance, October, 1995, p.60-62.
- ASTM B88, Standard Specification for Seamless Copper Water Tube, the American Society for Testing and Materials, Philadelphia, PA, Vol 2.01.
- ASTM B828, Standard Practice for Making Capillary Joints by Soldering of Copper and Copper Alloy Tube and Fittings, the American Society for Testing and Materials, Philadelphia, PA, Vol 2.01.
- Internal Corrosion of Water Distribution Systems, AWWA Research Foundation cooperative report, 1985 ed., Chapter 5, p.231-268.
- Safe Water Drinking Act, PL 93-523, December 16, 1974.
Safe Water Drinking Act, 1986 Amendments, PL 99-339, June 19, 1986. - Federal Register (56FR 26548) Final Lead and Copper Rule, June 7, 1991.
- Copper Brass Bronze Product Handbook, Copper Tube for Plumbing, Heating, Air Conditioning, and Refrigeration, 1986, The Copper Development Association, New York, NY.
- Cohen, A., Corrosion by Potable Waters in Building Systems, Materials Performance, August, 1993, p.56-61.
- Prevention and Control of Water-Caused Problems in Building Potable Water Systems, TPC Publication No.7, 1980, National Association of Corrosion Engineers, Houston, TX.
- Rossum, J.R., Pitting in Copper Water Tubing, Journal AWWA, Research and Technology, October, 1985, P.70-73.
- Wagner, J., Jr., and Young, W.T., Corrosion in Building Water Systems, Materials Performance, October, 1990, P.40-46.
The NALCO Water Handbook, Nalco Chemical Company, McGraw-Hill Book Company, New York, NY, 1979, p.2-1 to 2-16. - Myers, J.R., and Cohen, A., Soldering Flux-Induced Pitting of Copper Water Lines, Materials Performance, October, 1994, p.62-63.